Cane Weaving
Being an intricate craft, cane weaving is both time and labour intensive. Depending on the complexity of the pattern, it can take our artisans anywhere between one and three days to finish weaving a single piece of our furniture.
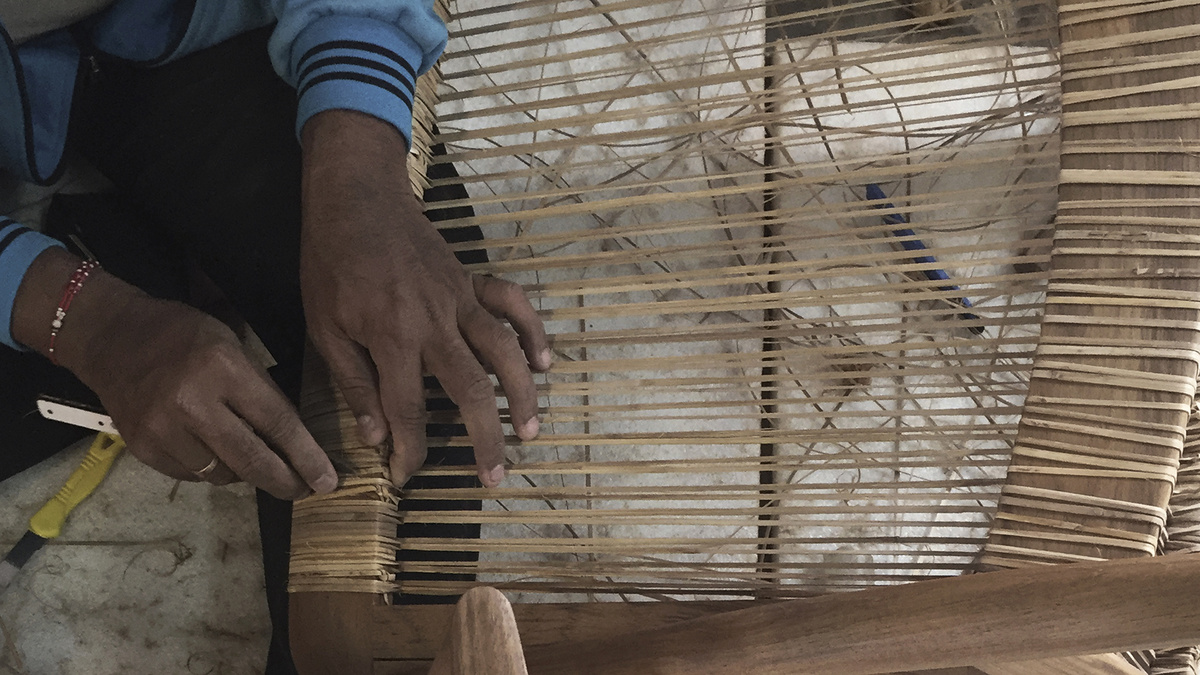
Cane weaving by hand is an integral part of our furniture. We do not use machine made cane or pre-woven cane; all our cane weaving is done 'on the wooden frame' by a skilled weaver. Our weavers are adept at weaving different types of patterns - diamond, cross or the unique Tangāli weave.
Our weavers hail from traditional weaving communities of Karaikudi (a town in the Chettinad region of Tamil Nadu), from Bangalore, and from Chennai. They bring decades of weaving experience and generational knowledge of the craft and material to our production process.
We source our cane from the north eastern part of India. Cane is obtained by peeling flat strips from the outer edges of rattan reeds. Cane is a resilient natural material and our handcrafted cane seats and backs can last for several years without sagging if they are used with a little bit of care.
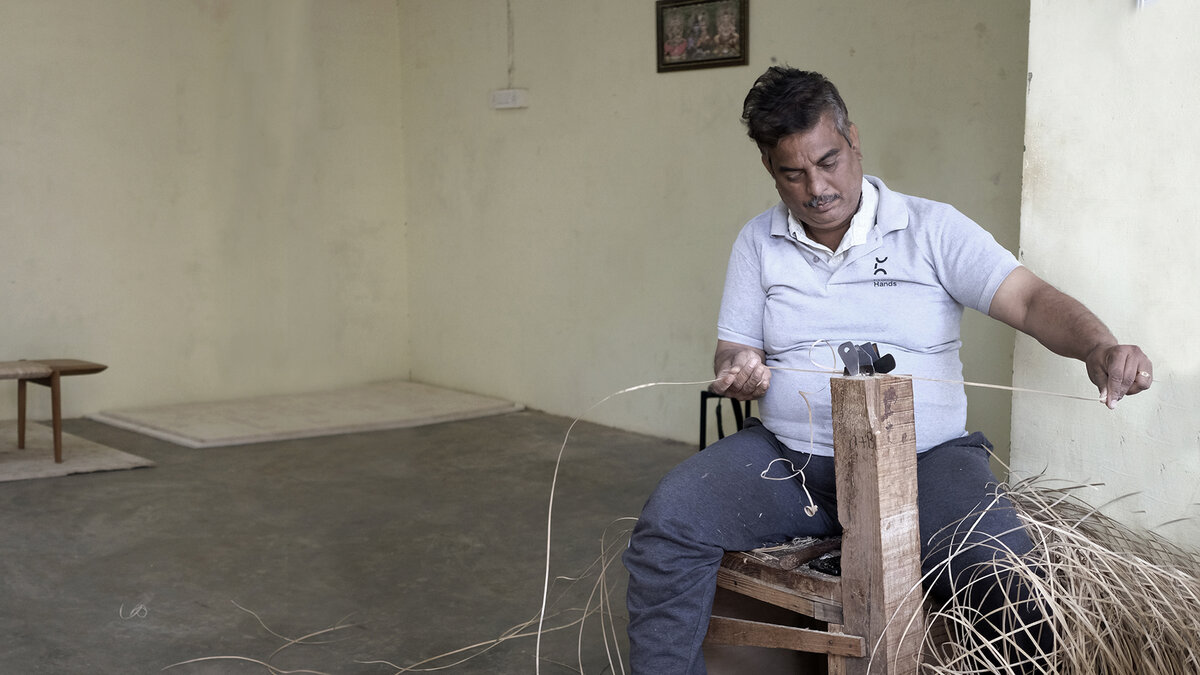
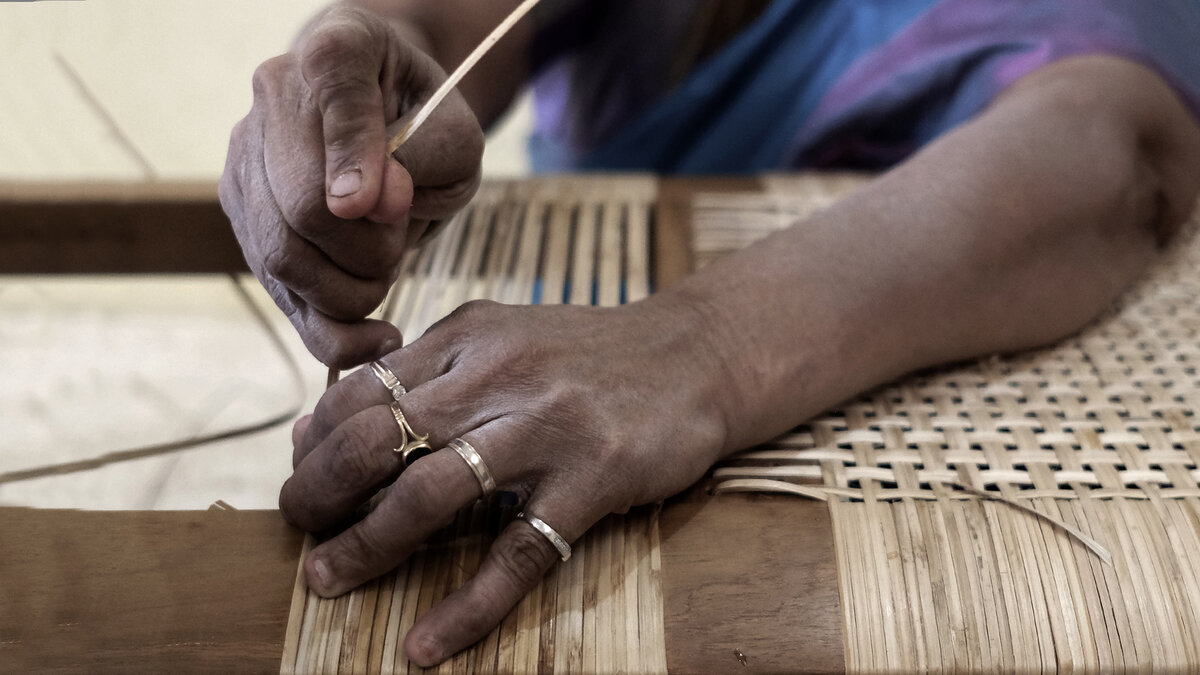
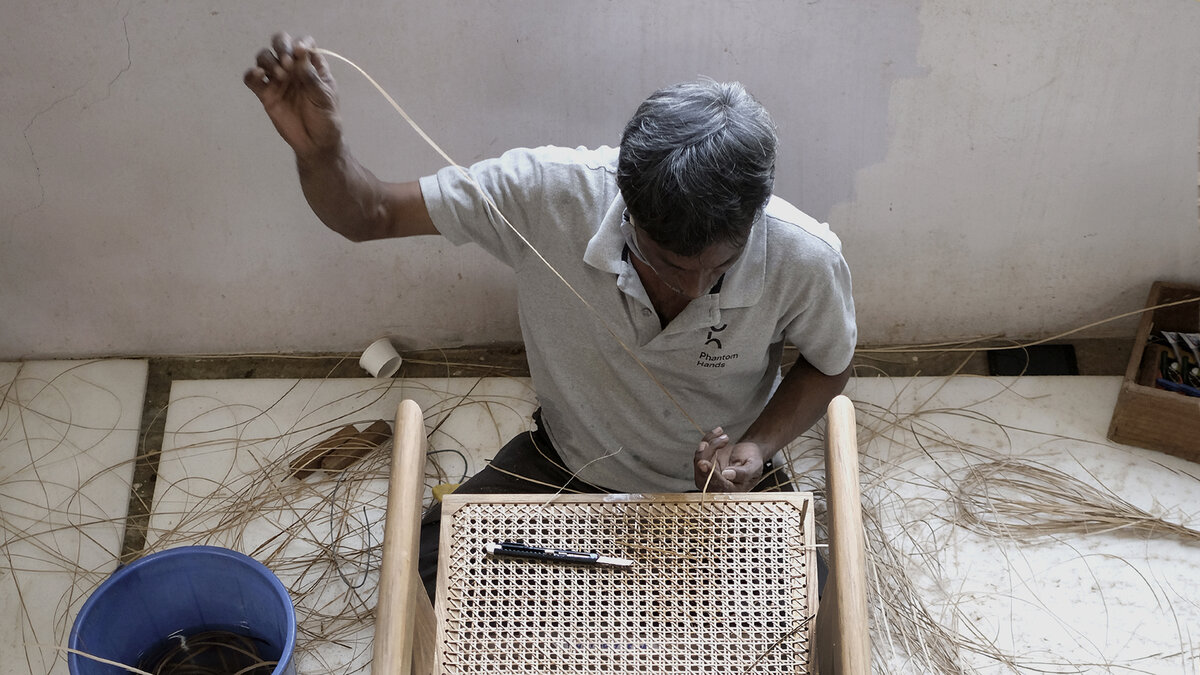
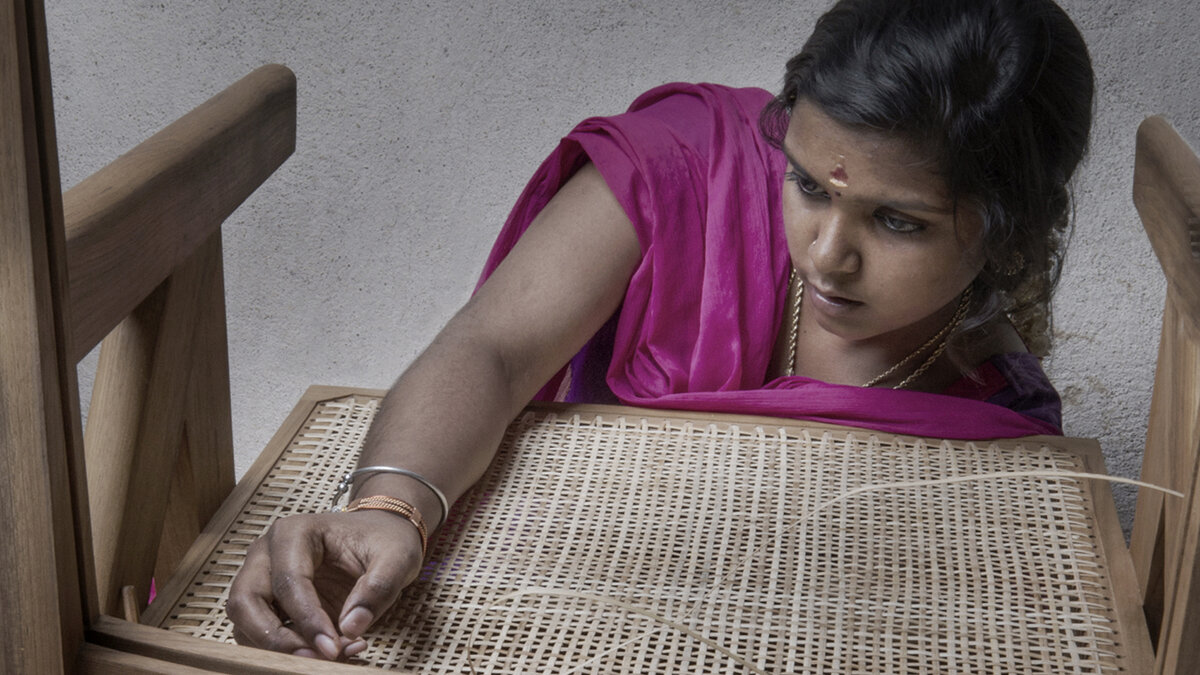
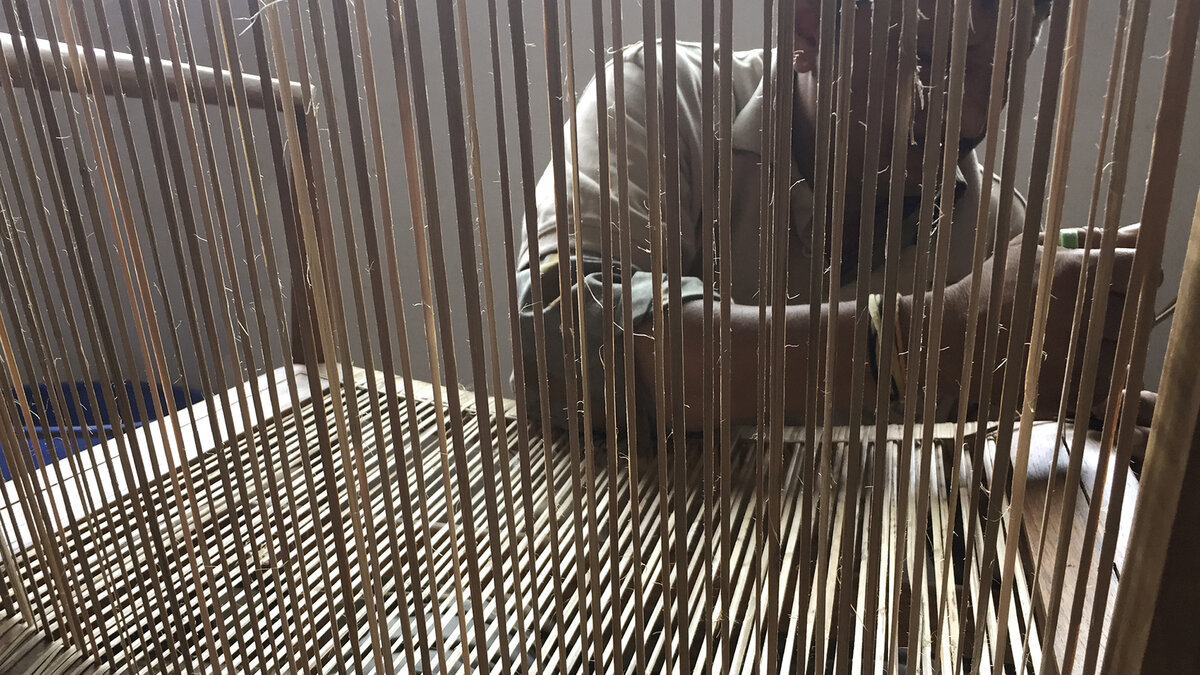
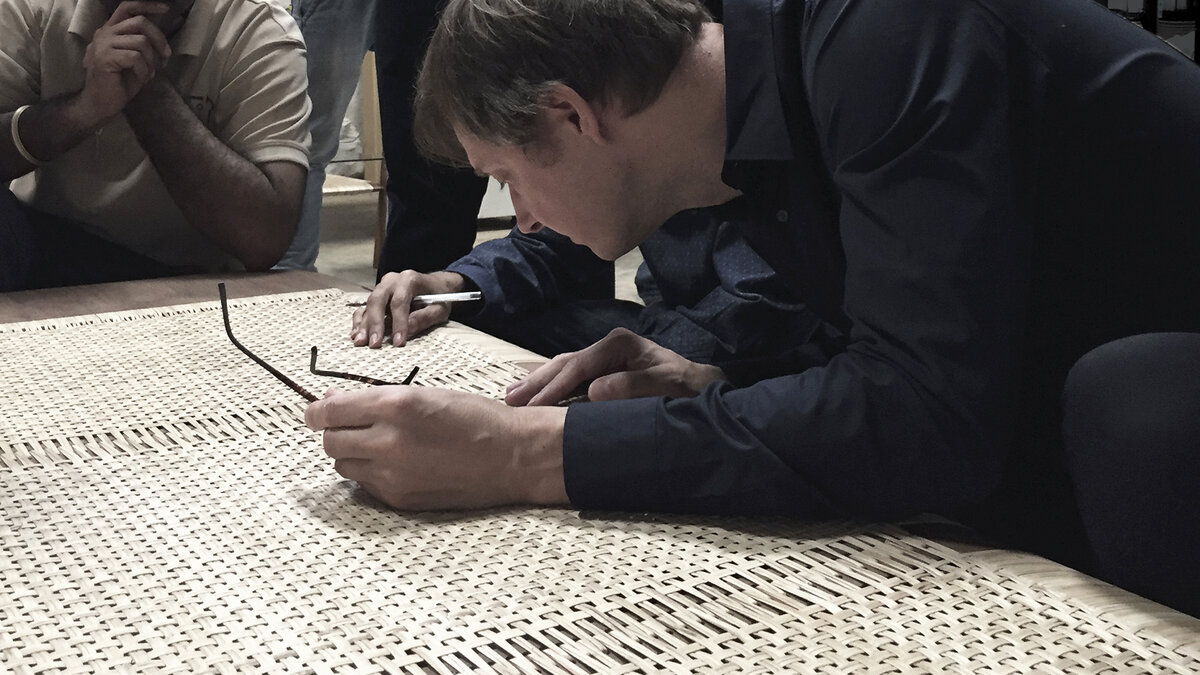